Tianda Chuzhou: A Breakthrough in Ultrasonic Inspection with Phased-Array Technology
Tianda Chuzhou transforms steel inspection with its new phased-array ultrasonic equipment, marking a significant advance in flaw detection. This project, completed in record time, highlights cutting-edge strategy and effective technical collaboration between Vallourec and Wuhan Zhongke.
By PM of Tianda
Vallourec Tianda Chuzhou has reached a crucial milestone with the introduction of its new phased-array ultrasonic production line, specifically designed to detect oblique injury in C90, T95, and C110 steels. This project, aligning with the new API 5CT standard, represents a significant advancement for the company and its commitment to premium product quality.
Rigorous Supplier Selection
PC-NDT (Non-destructive testing) experts and the NDT team of Tianda Chuzhou, fully supported by their executive team., decided to launch a new ultrasound project to meet current technical and regulatory challenges.
After evaluating factors related to technical difficulty, cost, project timeline, and equipment maintenance, Wuhan Zhongke, a scientific and technological enterprise and a nondestructive testing equipment manufacturer, was selected as the primary supplier.
Given the technical difficulty of the new phased array ultrasonic equipment, the project team took the initiative of organizing a meeting between PC-NDT, the Tianda Chuzhou NDT team and the Equipment Department and Wuhan Zhongke to overcome the technical challenges posed by the new equipment.
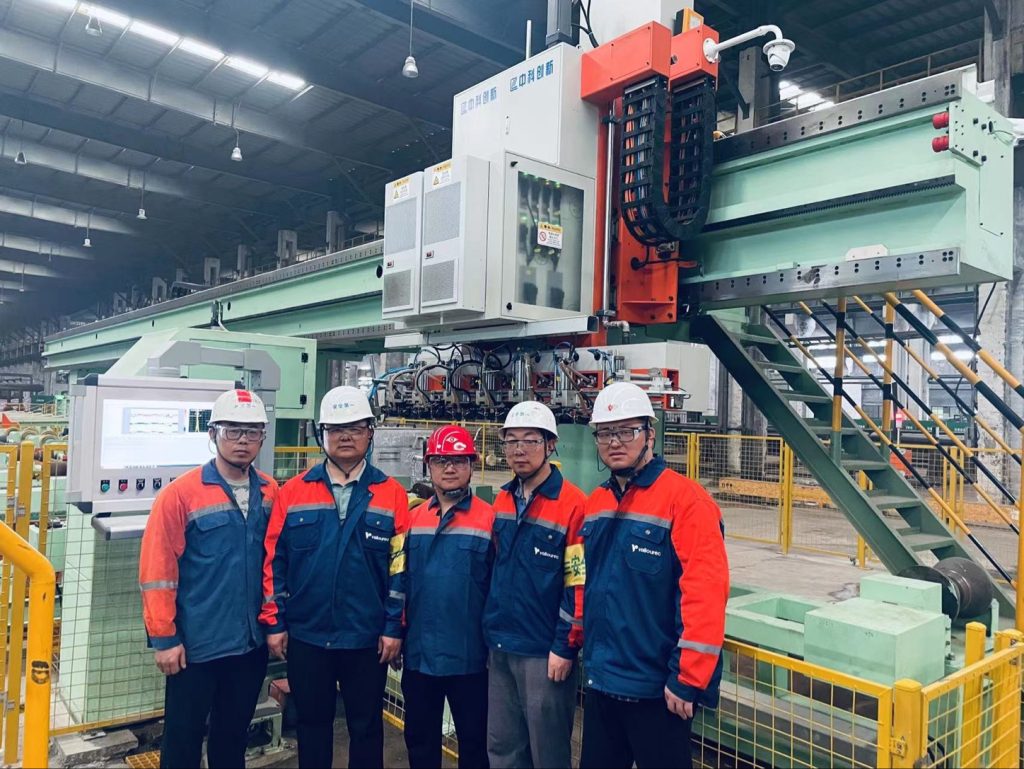
Collaboration and Technical Problem Solving
During the acceptance phase at the supplier’s facility, Wuhan Zhongke faced major technical hurdles. Through close collaboration and rapid communication between the project team, the Group experts and Wuhan Zhongke’s R&D technical team, the issues were resolved, allowing the project to be completed in record time.
In December 2023, following a series of rigorous tests, including a plant acceptance test in Wuhan Zhonghe plant performed by our Chinese NDT team, the equipment was installed and commissioned at Tianda Chuzhou’s Quality Inspection Workshop 140. The performance indicators of the equipment finally met the technical requirements, as validated by Michel Vahé, the EH region’s NDT expert, in February 2024.
At the end of April, the project guidance committee met and unanimously decided that all performance indicators for the new phased array ultrasonic equipment met requirements, and that the on-site acceptance test had been successfully passed.
A Success Story in Localization Strategy
Completing this project in just 15 months, compared to the usual 24 months for similar projects, is a remarkable example of Tianda’s capability in managing large-scale projects. This achievement also underscores the success of the company’s localization strategy for ultrasonic equipment and spare parts, reducing costs and enhancing long-term maintenance.
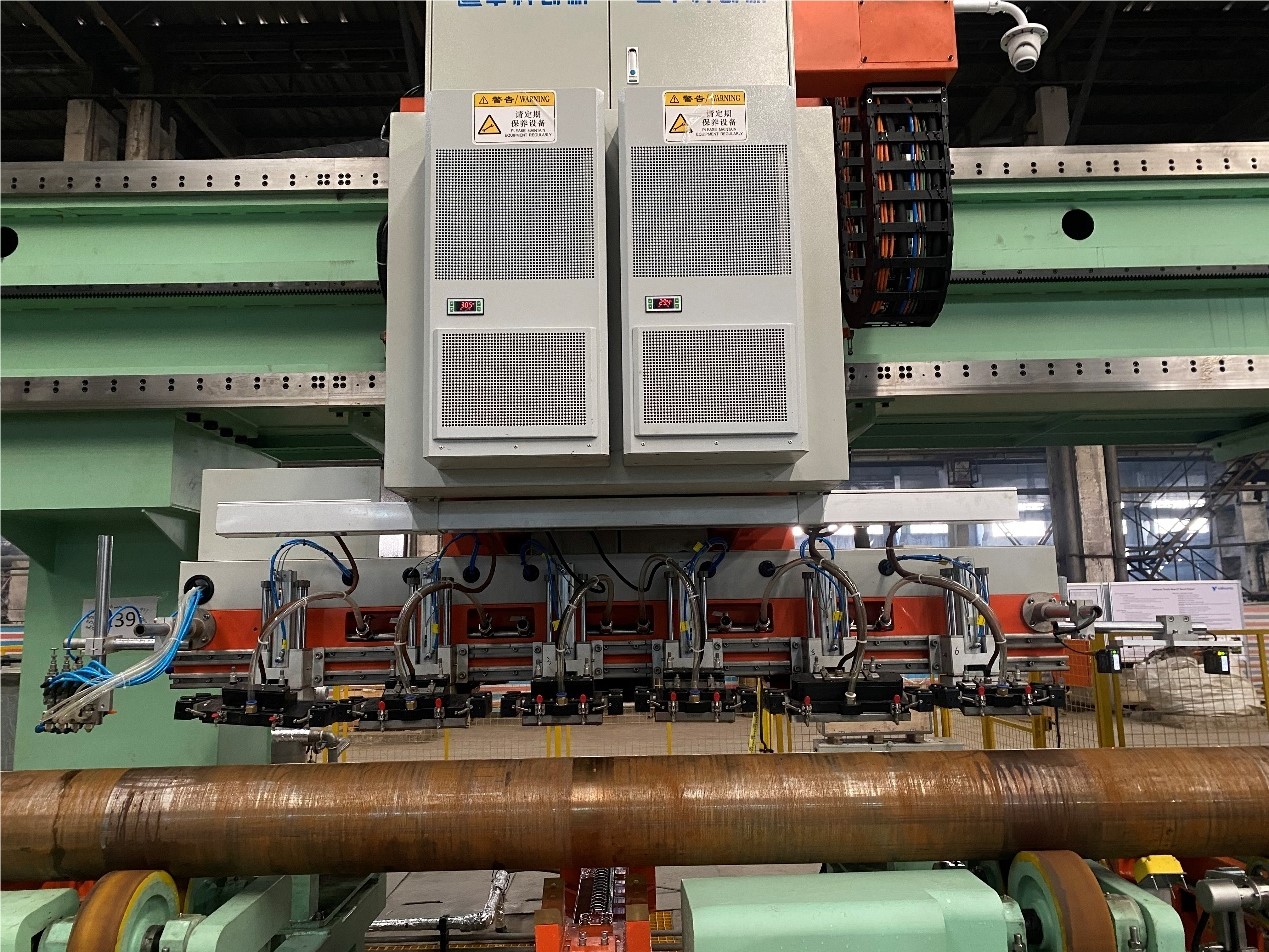
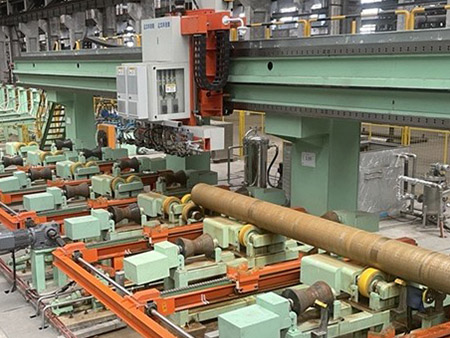
Towards Long-Term Collaboration
The success of this project paves the way for strengthened collaboration with Wuhan Zhongke for the development of other essential spare parts and maintenance services for Tianda Chuzhou but also for the whole Group. The equipment provided matches the performance of industry giants like General Electric and Olympus, while offering significant advantages in cost and project cycle.
Strategic Advancement in Ultrasonic Inspection
The successful acceptance of this equipment marks an important step in Tianda’s premium strategy. The phased-array technology allows for precise detection of diagonal flaws, flaw detection coupling monitoring, and thickness measurement, meeting the stringent requirements of high-end customers such as TotalEnergies.
The equipment is currently undergoing optimization and is preparing to face future challenges in its best possible condition. This advancement reinforces Tianda’s position as a leader in ultrasonic inspection and demonstrates its commitment to industrial excellence.
Key Features of Phased-Array Inspection
- Oblique Flaw Detection: Precise identification of anomalies in C90, T95, and C110 steels.
- World-Class Performance: Comparable to equipment from General Electric and Olympus.
- Cost and Maintenance Advantages: Cost reduction and improved maintenance through local collaboration.
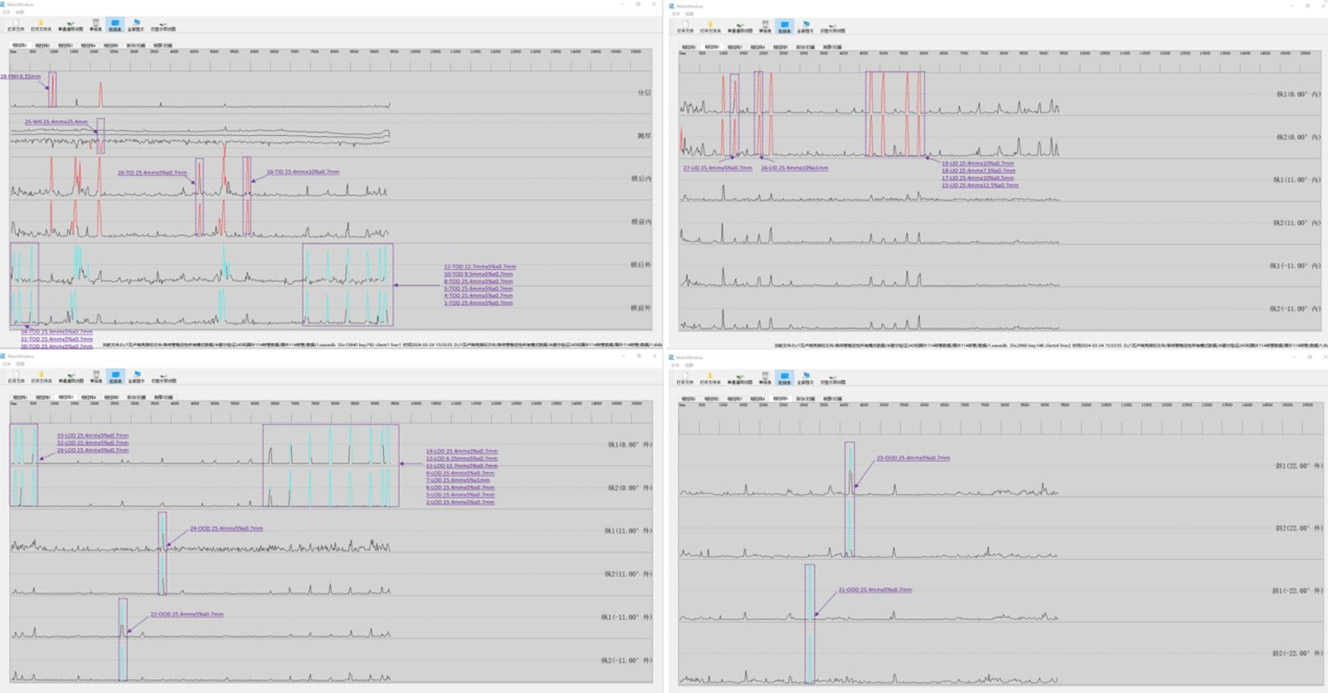